Blogs Detail
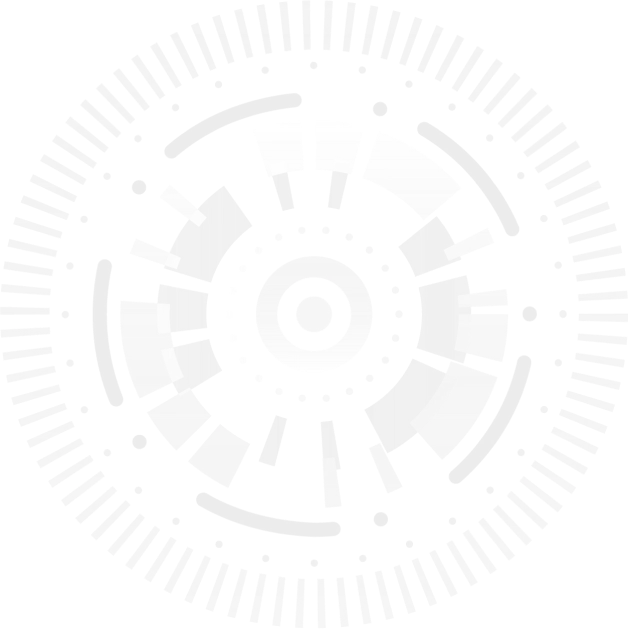
Challenges and Innovations in Industrial Robotics Programming
Written by
Admin
Posted On
10/28/2024 18:16:19
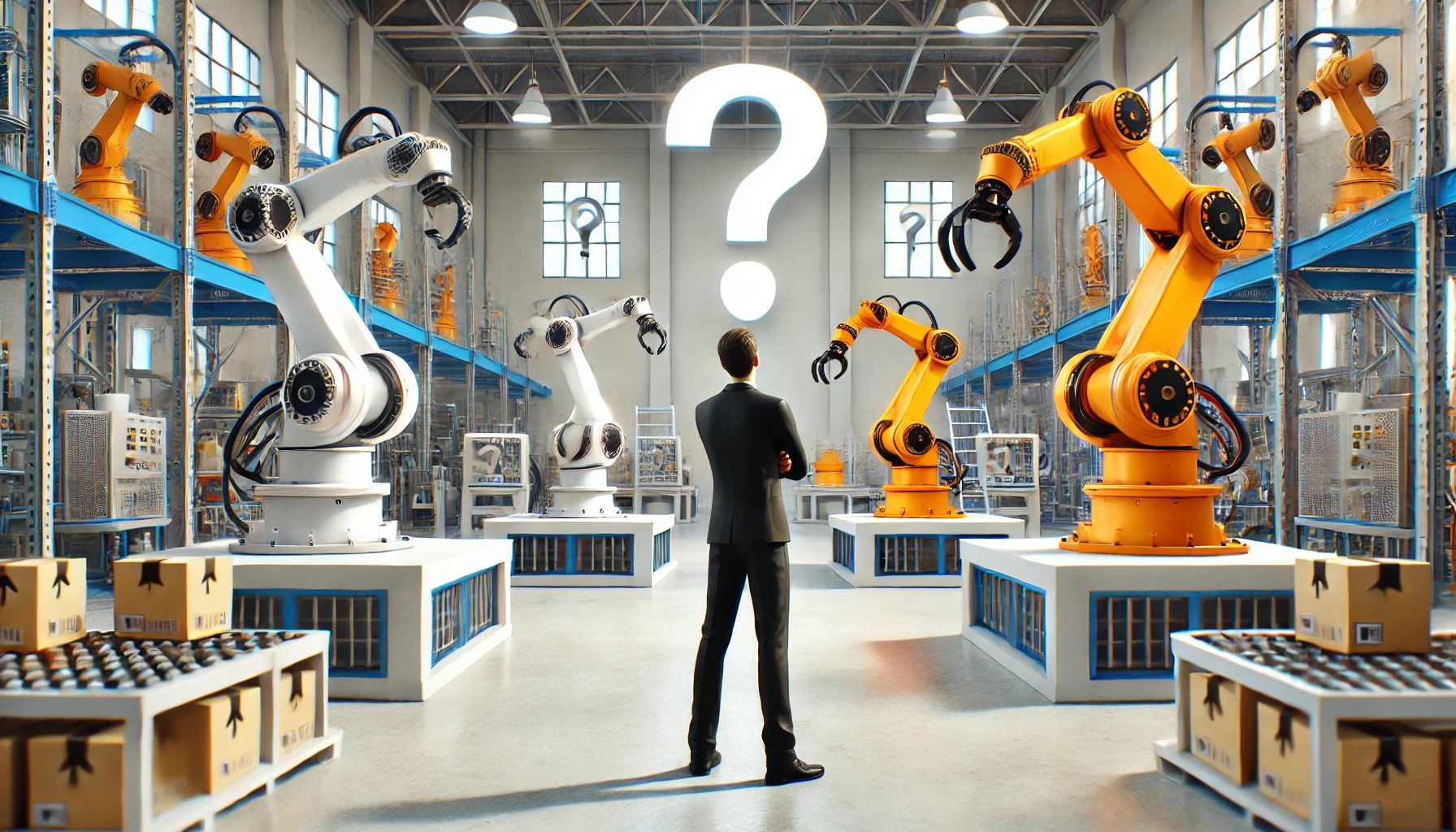
Key Challenges in Industrial Robotics Programming
1. Proprietary Programming Languages
Robotics programming is a fragmented landscape, with each major manufacturer—such as KUKA, ABB, and Fanuc, using proprietary languages (e.g., KUKA’s KRL, ABB’s RAPID) that are often incompatible with one another. This siloed approach makes it challenging for engineers to work across multiple platforms, limiting flexibility and complicating the integration of mixed-brand robot fleets.
Example: A manufacturer with both KUKA and ABB robots may face difficulties in creating a unified automation solution, as each robot requires specialised programming knowledge. For smaller companies, this presents a substantial challenge, as hiring engineers proficient in multiple languages can be costly, and training staff on diverse platforms is time-consuming. The lack of standardisation often leads to a dependence on platform-specific expertise, increasing project costs and lengthening timelines.
2. Limited Remote Access and Control
While remote access to robots is technically feasible with certain brands like KUKA, many robotic systems lack comprehensive remote connectivity, complicating off-site diagnostics, troubleshooting, and software updates. For smaller companies without in-house robotics staff, this limitation can create significant obstacles, especially when minor adjustments or diagnostics could otherwise be done remotely.
Example: Imagine a small manufacturing facility experiencing an intermittent fault on their robotic system. Without adequate remote access, the only recourse may be on-site troubleshooting, which is costly and delays production. For businesses operating on thin margins, these delays can have serious financial repercussions.
3. Complexity in Safety Integration
Safety is paramount in industrial robotics, but meeting these safety requirements is often complex and highly dependent on each application’s specifications. Programmers must account for precise end-effector movements, emergency stops, restricted zones, and compliance with industry standards like ISO 10218. Safety programming not only requires technical skill but also extensive on-site validation to ensure that robots function reliably without endangering operators.
Example: An automotive manufacturer may need a robotic welding cell that conforms to stringent safety guidelines. While the majority of the programming can be completed off-site, final safety adjustments and validation must occur on-site, involving fine-tuning based on real-world positioning and workspace specifics.
4. High Costs of Customisation and Reconfiguration
Industrial robots are designed for adaptability, yet reprogramming or customising them to perform new tasks often requires significant expertise. Customisation can become an expensive process when each change mandates substantial reprogramming. This limits smaller companies’ ability to adapt their automation setups for new projects or production lines, as each new task requires fresh code rather than simple configuration changes.
Example: A small electronics manufacturer may use a robotic system for component assembly. If they introduce a new product line with different assembly requirements, the robot will need to be reprogrammed—a task that often requires external expertise due to the proprietary language and complex nature of the application.
Innovative Solutions in Robotics Programming
1. Modular Programming for Flexibility
Modular programming is gaining traction as a solution to the high costs of reconfiguration. By creating reusable software modules, engineers can quickly adapt robots to new tasks without starting from scratch. Modular code libraries specific to certain tasks (e.g., pick-and-place, welding) allow companies to modify and deploy applications with minimal programming knowledge, reducing dependency on external integrators.
Example: A food packaging company could use modular programming to repurpose an existing robot from filling bottles to boxing products, simply by switching out one module for another. This flexibility makes it easier to respond to changing demands and enhances the robot’s value.
2. Enhanced Connectivity and Remote Diagnostics
With advances in IoT and connectivity, some robotics platforms now offer improved remote diagnostics and control capabilities. This innovation allows engineers to access and troubleshoot robotic systems from anywhere, reducing the need for costly on-site support. For companies using KUKA robots, for instance, remote configuration is feasible, allowing engineers to handle most programming, configuration, and diagnostics off-site. While not universally available, this capability is an important step toward more flexible and scalable robotics solutions.
Example: A packaging facility facing intermittent connectivity issues with their robotic system can have an RAEaaS engineer access the system remotely, diagnose the problem, and make necessary adjustments without requiring an on-site visit, saving both time and cost.
3. Low-Code and No-Code Robotics Platforms
To make robotics more accessible, low-code and no-code platforms are emerging, enabling individuals without advanced programming knowledge to configure robots for specific tasks. These platforms simplify complex coding requirements and can be especially beneficial for small businesses that need flexible robotics solutions but lack the budget for full-time engineers.
Example: A small-scale manufacturer might use a no-code platform to set up a robotic arm for simple assembly tasks. By dragging and dropping pre-configured actions, they can set up automation with minimal training and investment, enabling more agile adaptation to new workflows.
4. Safety Simulation and Virtual Commissioning
Safety simulation and virtual commissioning technologies allow engineers to test and refine safety protocols in a virtual environment before deploying them on the factory floor. By using digital twins and advanced simulation tools, companies can verify safety settings, optimise robot paths, and identify potential risks ahead of time, reducing on-site commissioning time.
Example: A pharmaceutical company implementing a robotic pick-and-place solution in a sterile environment can use virtual commissioning to ensure the robot’s movement does not cross contamination boundaries. This reduces on-site setup time and minimises disruptions during deployment.
Conclusion: Balancing Innovation with Practical Application
Industrial robotics programming is advancing, yet significant challenges remain, especially for smaller companies navigating the complexities of proprietary systems, limited remote access, and stringent safety requirements. By embracing modular programming, enhanced connectivity, and simulation tools, RAEaaS aims to bridge the gap between high-quality robotics expertise and the practical needs of small to mid-sized companies.
Through RAEaaS, clients gain access to innovative solutions that minimise costs, improve adaptability, and ensure safe, efficient robotic operations, without the long-term commitment or high overhead of traditional integrators. As the field of robotics continues to evolve, RAEaaS stands at the intersection of innovation and accessibility, bringing the latest programming advancements to companies that might otherwise be left behind in the automation wave.
Tags:
Industrial Robotics Programming Proprietary Languages ABB Robotics KUKA Programming Robot Diagnostics Automation Challenges Remote Troubleshooting Robotics Integration Advanced Manufacturing Robotic Safety Protocols Custom Automation Software Engineering Complexity Modular Programming Robotics Innovation Manufacturing Solutions